Improving Performance with STEP Survey™
APS’ unique STEP (Site Test for Enhanced Processing)™ Survey is a logical and methodical three ‘STEP’ process to problem solve, test solutions, and engineer a response. It evaluates production chemistry, process engineering and production operations to determine the optimum solution, to maximise production capacity from existing resources.
What differentiates the STEP Survey™ from other facility reviews is APS’ ability to characterise and quantify the impact of any potential process optimization in real time using real production chemistry. This is only possible using APS’ patented ‘Dynamic Flow Flotation Test’ (DFT) test rig. The equipment enables highly trained APS personnel to fully evaluate and illustrate the potential impact of full-scale upgrades and thereby de-risk potential capital investment.
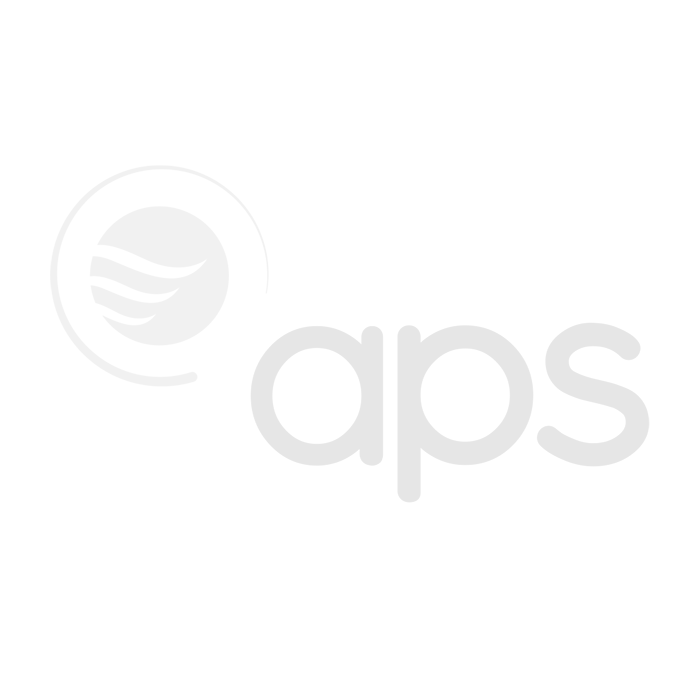
On site data collection, including:
Produced Fluid Characteristics (composition & emulsion tendencies)
Production Chemistry (water treatment chemistry, phase separation, flow assurance
& flow integrity)Process Configuration
Equipment Design & Performance (fluid stream characteristics,
design v actual, design limitations)System Operation (operating practices, troubleshooting & maintenance)
Review of chemical and
process data, including:
Root cause analysis of issues
using information gatheredProcess performance review
using an ATEX Zone 1 certified
Visual Particle Analyser (ViPA),
to determine particle size
distribution, oil droplet, solid
particle & gas bubble concentration
trends in live fluidsProduced Water Treatability
testing for Best Available
Techniques (BAT) and Best Environmental Practices (BEP)
using static jar testing and patented Dynamic Flow Flotation TestingReal-time data collection correlated
to system process conditionsDetermine synergy between production chemistry and
enhanced gravity separationDetermine if individual or multiple
gas bubble size range is required
Detailed design treatment options, including:
Development treatment strategy
and engineer solutions to address essential management of the challenging fluidsIdentify optimum bubble sizes,
range and injection locationsSmall-scale offshore technology assessment de-risks investment
in large scale MiFU pilot trialsDetailed client report
Fully costed options for multiple
rental (opex) or permanent
upgrades (capex) solutionsPilot unit trials de-risks capital projects for permanently installed solutions